ENSURING THROUGHPUT IN POLAND
Complex Pipeline Refurbishment Program
Delivers Major Gains
Dec 08, 2014 + + + Keeping hundreds of miles of Poland’s pipelines flowing
at optimum capacity isn’t easy. It’s a demanding job, requiring great care
and attention to planning and executing the rigorous maintenance programs
necessary to ensure that every line is clean and free of defects,
especially those that could eventually cripple production. A recent
pipeline refurbishment program carried out by a major gas transmission
operator in the mountains of eastern Poland, along the Ukraine border,
illustrates the complex nature of maintaining pipelines.
In keeping
with its commitment to maintaining the integrity of Poland’s gas
transmission system, the operator commissioned a comprehensive cleaning
and inspection of a 28-inch diameter, 11 km (6.8 mi) section of a 40 km
(24.8mi) pipeline, which was commissioned in the early 1970s. The
pipeline, which is part of Poland’s natural gas network, is particularly
important because it can support an interconnector to and from the
Ukraine.
Having partnered on many pipeline operations over the last
20 years, T.D. Williamson (TDW) was commissioned to execute the program,
which was completed in August 2014. As a result of the complex pipeline
cleaning, gauging and inline inspection (ILI) activities, the operator
reaped a number of benefits, including increased product flow and enhanced
pipeline integrity.
The advantages to the operator are
far-reaching. Because the line is clean and free of debris that impeded
flow, there is a much higher flow rate. This means that associated
production costs are lower and transmission is more efficient. Looking
ahead, the operator’s repair costs will also be reduced because the ILI
data produced by the inspection flags defects, making it possible for the
operator to address them as needed. Potential damage otherwise incurred by
these defects is mitigated, reducing future associated maintenance costs
and downtime.
Cleaning, gauging & inspecting
When TDW was
contracted to clean the 28-inch diameter line that runs through the Polish
mountain range, the line was operating at a pressure of 38 barg, at an
average flow of 75,000 m2 per hour. It was deemed unpiggable because it
was so choked by debris that a pipeline cleaning or inspection pig would
be unable to pass. Further complicating the situation, a visibility study
carried out by TDW before cleaning and inspection revealed a section of
the line with eight acute miter bends, making it impossible for the pigs
to navigate and clean, let alone inspect.
Working in cooperation
with the operator, TDW developed a solution. To address the problem,
custom-designed temporary pig launchers and receivers were built and
welded at strategic points along the line. To prevent a pig from being
lodged in the miter bends, these sections were removed and replaced with
pipe that would accommodate the cleaning and inspection pigs. All pigs
scheduled for use during the program were fitted with transmitter units
that the crew would use to track their progress. Finally, to verify the
piggability of the line and ensure that its cleaning pigs and inspection
tools would be capable of negotiating the pipeline, TDW performed a gauge
pig run. Once this was successfully completed, preparations were made to
proceed with the first of the cleaning runs.
Efficient cleaning
clears the way
To clean the lines, a five-step cleaning program was
carried out by TDW with 24 specially selected cleaning pigs. After
completing 23 runs, the 11 km (6.8 mi) line, which had been so congested
it was unpiggable, was clean and free of debris. Before cleaning,
production had been sluggish. As a result of the cleaning, TDW cleared
approximately 3.5 tons of silt, timber, metal fragments, welding rods and
pipelaying equipment, allowing gas to flow much more freely.
Satisfied that the line had been thoroughly cleaned, TDW proceeded with
the next phase: an inline inspection of the 11 km (24.8mi) section of the
line. Working closely with the operator‘s team, TDW executed inspection
runs on the line during a three-week period in August 2014. TDW used a
number of its high-resolution inspection tools to inspect the pipeline,
including deformation (DEF) technology for geometric anomaly inspection,
Gas Magnetic Flux Leakage (GMFL) inspection technology for corrosion
inspection, and the XYZ Inertial Measurement Unit for GPS pipeline
mapping.
Following data validation and analysis, TDW delivered a
comprehensive final report to the operator. After assessing the condition
of the pipeline, as reflected in the ILI data, the operator will work with
TDW to formulate plans to schedule any necessary repairs or further
procedures on the line. The operator and TDW are currently discussing how
this method of cleaning and inspection might be scaled and carried out on
the remaining 29 km (18 mi) section of this line.
The final outcome
of the pipeline refurbishment program is extremely important to the
operator and its efforts to assure the continued integrity of the line.
“Much of the success of this program lies in the painstaking attention to
inspecting the line before cleaning,” says Mateusz Bil, Project Engineer
for TDW. “This is critical because it allows us to rectify trouble spots,
such as the eight miter angles that would most certainly have blocked the
cleaning pigs, disrupting the cleaning operation. Instead, we were able to
clean the line so that it was in pristine condition, ready for the inline
inspection. By doing so, the inspection runs would generate the highest
quality of data, revealing potential threats to pipeline integrity,” he
added.
Source: T.D. Williamson Polska Sp. z o.o.
www.tdwilliamson.com
|
 Worldwide more than
90,000 paid subscriptions
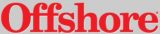 Worldwide
more than 48,000 subscriptions - 100% one-year direct request
qualification
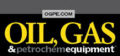
'What's New' in Upstream, Midstream and
Downstream Products & Services. Circulation 37,000
PennWell Petroleum Group:
Oil & Gas Journal
Oil & Gas Journal Russia
OGJ_eNewsletter OGJ-Website-Statistics
Oil, Gas & Petrochem Equipment
Offshore Magazine
Offshore
Russia
Offshore eNewsletter
Offshore
Website Statistics
Oil & Gas Financial Journal
+ + +
For more information, media
kits or
sample copies please contact
Andreas
Sicking +49 (0)2903-338570
wilhelms@pennwell.com
www.sicking.de
|