The future for protected pipelines
February 2012 saw a gathering of world experts in Vienna at AMI’s Pipeline Coating
2012. The conference kicked off with leading AMI market consultant Noru Tsalic, who outlined the growth expectations for steel pipe coatings including annual growth rates of around 5% amounting to 450 million square metres in 2013. Gas pipe coating is by far the largest sector amounting to 74% of the total, with oil pipelines at 21% while the water industry uses about 4%. The rise in volume of coating demand is partly due to changes in geographical consumption and sourcing. There will be developments in global regional demand for oil: by 2030 global oil consumption is predicted to rise to 4600 Mtoe and Asia-Pacific will consume around 40% compared to 30% in 2000, while at the same time demand in Europe will decrease in proportion. The situation is similar for gas, with Asia-Pacific using around 12% of the 2100 Mtoe of global consumption in 2000 and this is expected to rise to 25% of the 4200 Mtoe utilised worldwide in 2030. The supply map will also change and Asia-Pacific will be delivering 30% of global gas supplies in 2030 compared to 12% in 2010. These trends in regional supply and demand are driving pipeline construction. In addition, oil and gas are being sourced from more remote and hostile areas, which require a denser coating to protect against corrosion, extreme temperatures and pressures. Thus the overall market for pipe coating is expected to grow.
In one case study, Gazprom Vniigaz looked at quality control of the coating for the Yamal-Europe pipeline using techniques such as ultrasound on site, and adhesive strength testing of different points on the pipe. It was proposed that coated pipe should be stored using wooden racks with a non-woven pad for protection and a surface cover. When joints are welded the polymer coating can melt and shrink, so Vniigaz looked at the temperature along the pipe: a protective shield and a clamp on the coating edge were found to be helpful in minimising the effects of the rise in temperature. Professor Protasov of the Gubkin Russian State University of Oil and Gas has examined the factors affecting the durability and service life of coatings under different operating conditions.
Riyadh in Saudi Arabia has been expanding at a much faster rate than was expected: 2.5 million inhabitants were expected in 2010 when in fact there were 5 million and this figure is rising. The city is facing water shortages if measures are not taken.
Borouge reports that over 900km of coated pipe of 48”-72” diameter are in construction to transport water in the Ras Al Zour-Riyadh pipeline from desalination plants on the coast with a scheduled completion date of Q1 2014. Some of the factors to be considered for the coating include surface temperatures of up to 70C and transport and handling over rough terrain. A 3-layer system was selected comprising a black HDPE topcoat, an MDPE grafted adhesive and a fusion bonded epoxy (FBE). Corrosion has been estimated to cost the Gulf States around US$2.2 billion in 2010 (NACE) and coating is a vital component in the region.
Polyurethane (PU) coatings are versatile as they can be applied in different thicknesses, using different chemistries and on site or in plant. They are typically applied over a 3-layer PE system.
BS Coatings has been in the business of pipe coatings since 1945 when the company Bitume Speciaux was created by TOTAL, Vallourec and Pont á Mousson and the Carboplast coating was patented. To date it has coated more than 100,000km of pipe. BS Coatings has compared PU coatings with epoxy for rehabilitation projects and found that it has a much lower drying time (1h vs 4h) and better mechanical properties. It has been tested in Subkha conditions: this is an Arabic term for coastal regions where soil has an 18% salt content and resistivity as low as 20 Ohm.cm. Specific electrochemical resistance was tested to Saudi Aramco specification 09-SAMSS-089. The material has also been tested for use in Russian cold climates.
Iran has over 30,000km of high pressure gas pipelines and there have been some issues with coating disbondment.
Safa Rolling and Pipe Mills company applies a variety of pipe coatings from 3-layer PE to PU and bitumen enamel and has studied the phenomenon of cathodic disbondment. It had been assumed that the issue was due to problems in manufacture, but tracing the failed pipes to the quality control results at the factory did not corroborate this. A variety of tests was carried out including an 80C hot water soak: disbondment occurred when the cathodic potential was high. The failure mechanism may be the accumulation of hydroxyl ions at the cathode, which react with the iron oxide on the steel surface to form hydroxide, increasing the pH on the surface in contact with the coating. This increases the stress in the coating, which is more critical for 3-layer PE as the PE layer is thicker and the thermal expansion differential is higher. There are several measures that can be taken to reduce this problem including better pipe surface treatment and careful monitoring of the cathodic voltage in service.
As discussed by Safa Rolling Mills, the factors that adversely affect epoxy bonding include heat and humidity, the cathodic protection current and residual stress in the upper coating layers of 3-layer systems. The adhesion of FBE has been improved by Dow Coating Materials using new technology to address these issues.
Berry Plastics has been looking at methods of field joint coating for PP-coated pipes. Damage to pipe coating can occur during field joint coating and operators like TOTAL, Saipem and Petrobras have specifications that hold subcontractors responsible for disbondment and require preventative measures to be taken. The options for joint coating include high temperature shrink sleeve, injection moulding, flame spray, fused tape systems and field film extrusion techniques. The Covalence shrink sleeve system includes a new dual adhesive system with one optimised for epoxy bonding and the other for polyolefin bonding. It has been used in the TOTAL Laggan Tormore pipeline and the MEW pipeline from Abullah WOC II Port to West Funaitees.
Operators have their own extensive research programme: Gasunie in the Netherlands has studied field joint coating for a new North-South pipeline running 600km across the country with a diameter of 48 inches. The line pipe was coated with 3-layer PE and the joint was specified as epoxy or viscoelastic for corrosion protection and a shrink sleeve for mechanical protection. Pipe for pressings and drillings were specified with a thick PP coating, which is 25% stronger than PE, and the field coat was matched - PP flame spray, Canusa GTS PP and PUPP lining (polyurethane layer, fibres and a PP plate).
Statoil has examined PU field joints. At the Asgard site cracks were observed, so the system was tested for 2 years in salt water at 140C. There was no steel corrosion, so the cathodic protection was working and there were no external signs of hydrolysis. At Gullfaks a similar situation was observed. The coatings were tested for accelerated ageing under a variety of conditions to ascertain service life, which should be at least 20 years.
The ideal heat shrink sleeve for 3-layer field joint coating, according to
Canusa CPS, combines epoxy, adhesive and a crosslinked polyolefin (either PE or PP). The force cure system was tested in the Waupisoo pipeline carrying bitumen from Fort McMurray to Edmonton.
KWH Pipe has been working in partnership with Borealis on a new field joint coating system, which has been used on the Gasum Oy Mäntsälä-Siuntio natural gas pipeline project in Finland by the subcontractor Stroytransgaz. The operating temperature of the pipe ranges from -30 to +30C and much of the installation took place in subzero conditions. The patented technique involves the equipment rotating around the pipe applying hot melt film of PE or PP, which requires a 400mm space. The process involves blast cleaning of the joint, the machine is then lifted onto the pipe and induction heating and FBE application take place, followed by polymer in a second induction step.
There are three main types of deep sea field joint coating: injection moulded polypropylene or polyurethane and elastomeric coatings.
Exova is involved in independent testing and quality control. Pipes are subject to extremes of temperature during installation such as heating during welding, re-heating for field joint coating, quenching in salt water and cooling during lowering to the ocean bed. They are also subject to physical stresses from winding and laying. All of these factors should be taken into allowance when designing a new pipeline and coating system.
A new polymer system for deep sea field joints is under examination by IFREMER (the French
Ocean Research Institute). The current materials have limitations – polyurethane by temperature and polypropylene by process. The new plastic is polydicyclopentadiene (pDCPD), trade name Telene. It has been subjected to simulated offshore accelerated ageing tests. Water absorption is low (less than 1%) and thermal conductivity testing at Exova in Canada shows that the material is okay after 6 months of ageing at 160C. The overall results indicate that this material is a candidate for field joint coating.
Denis Melot at TOTAL has been working with IFREMER on lifetime prediction of subsea wet thermal insulation coatings, which are complex. The anti-corrosion layer is FBE, which can be tested with NACE, ISO and NORSOK standard methods. There are no standards for other aspects such as the bonding of the insulation to the FBE, so TOTAL has its own procedure: GS COR 226, before and after ageing. The thermal insulation reacts with the anti-corrosion paint and the field joints. Ageing is tested at the maximum rated temperature, 15C and 30C below that and at 4C. One of the major causes of failure of insulation is poor application and quality control. Trelleborg Offshore offers thermal insulation of pipes.
Polypropylene is increasingly being specified in offshore pipe coatings. PETRONAS Research in Kuala Lumpur, Malaysia has been developing a new 3-layer PP coating system to cut costs and the challenge is to improve the toughness of the polymer. Wasco Coating provided facilities for the coating trials and PETRONAS Carigali supplied the pipes. The top coat comprised Propelinas PP, toughening agents and stabilisers, while the adhesive interlayer comprised PP modified with MAH, and a commercial FBE was used directly on the pipe. Standard tests were carried out on coated pipe, for example there was no coating holiday at 25kV, peel strength was 3-times the DIN requirement at 50C and thermal ageing to 2012 showed no embrittlement.
DuPont has a new internal coating for downhole tubing, where there are issues with clogging due to asphaltene, paraffins and scale forming deposits. StreaMax is based on fluoropolymers and is stable under operating conditions of 260C. A thicker coating (100-180 microns) is recommended for areas with asphaltene or wax and these were tested in an Alberta field at 5800 feet deep. After 21 days the pipes were withdrawn and showed no deposits. In a well with severe asphaltene problems, no cleanups were needed during 6 years of operation, while the reference well requires cleanup every 2 months.
The viscoelastic coating supplied by Kleiss & Co. B.V. is based on polyolefin, impermeable to moisture and oxygen, and adheres without a primer. It has been tested at Charter Coating and on a water pipeline in the Kingdom of Saudi Arabia.
Protective casings around pipelines are subject to corrosion and this can be treated using filler. A good material will be anti-corrosive, water resistant, dielectric, inert and pliable. There are many standards for pipes in the US including Department of Transport (DOT) CFR, PHMSA and NACE. The NACE standard SP0200-2008 describes petroleum-based compounds. Trenton Corporation has provided over 3 million litres of wax filler worldwide: current procedure is to evacuate water, add a corrosion inhibitor and then fill.
One of the complications for the industry is the need for pipe in different global regions.
Bredero Shaw has developed a new system whereby a mobile coating plant can be set up rapidly (trade mark Brigden). The plant is packed in ISO compliant containers ready for shipping including conveying, tunnel and cooling towers. Plant 1 was set up in 9 weeks and can coat pipe from 8” to 42” diameter.
The next networking event, AMI’s conference on Pipeline Coating 2013, is scheduled for February in Vienna, Austria. The call for papers ends in the summer of 2012, so please send paper offers to Dr. Sally Humphreys before then, email
sh@amiplastics.com
Source: Dr Sally Humphreys
Business Development Manager
Applied Market Information Ltd, AMI House, 45-47 Stokes Croft, Bristol, BS1 3QP, UK
Email: sh@amiplastics.com
Web site: www.amiplastics.com
|
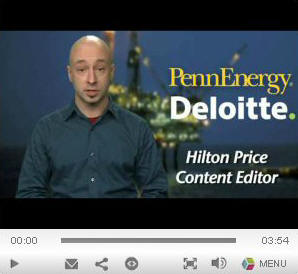 Video:
PennEnergy
Weekly Newscast .
+
+ Media Links + +
For more information, media details or
sample copies please contact
wilhelms@pennwell.com
www.sicking.de
|