Element: Oilfield Engineering with Polymers Extreme
conditions drive materials advances in oil and gas
Failure is not an
option when a part is at the bottom of the ocean, deep in the earth or
many miles away in the desolate desert or frozen wastelands, but all of
these hostile situations are becoming more common operating conditions for
the oil and gas industry. The cost of the safety-critical components is
minor compared to the cost of an oil leak or a well shut down, so the
highest quality standards and performance are demanded from suppliers. The
role of polymer materials in the oil and gas environment will be discussed
at the 9th international conference Element Oilfield Engineering with
Polymers organised by AMI in London at the Millennium Gloucester Hotel
from 21-23 October 2014.
The industry needs
high quality and high standards, with assessment of life time to maximise
reliability, while the research and development divisions of the major
operators and their suppliers are constantly looking for the ultimate
durable materials for applications ranging from seals and sealing to
insulation, flow lines, risers and coatings. In France, TOTAL
has been
working with IFREMER testing qualification and lifetime prediction methods
for subsea wet thermal insulation coatings, which are being used at
increasing water depths. From Scandinavia, STATOIL, NTNU and SINTEF
have
collaborated on ice-phobic coatings to reduce slip and to prevent ice from
forming and hindering functional equipment, which are particular issues in
arctic conditions.
The Hoerbiger
Corporation of America is studying lifetime prediction methods for
critical components in oil and gas. Greene, Tweed and Co. in the UK is
employing the Arrhenius techniques of life estimation in their elastomer
and seals division. O-ring seals in drilling applications are the subject
under study by BAKER HUGHES using compressive stress relaxation and
accelerated ageing methods and QUADRANT EPP has looked at the use of
polyamide-imide (PAI) in labyrinth compressor seals.
The operator STATOIL
has been working with ELEMENT MATERIALS TECHNOLOGY
HITCHIN using fracture
mechanics to examine life extension of tension leg platform (TLP)
flexelements. ELEMENT conducts a range of evaluation tests and research
into oilfield polymer materials. From the polymer industry, VICTREX, a
leading PEEK supplier, has looked beyond the NORSOK M-710 standard for
lifetime prediction of high performance polymers.
In the oilfield it is
not just wide temperature ranges that are encountered, but also chemicals,
gases, pressure and mechanical forces. The behaviour of FKM elastomers in
hydrogen sulphide has been studied by JAMES WALKER & Co.,
while SAINT-GOBAIN has reviewed seal material
selection for aggressive environments. One of the oldest companies supplying this area,
DUPONT, has
high performance polyimide and perfluoroelastomers for high pressure high
temperature (HPHT) applications. From Japan, DAIKIN has a new
fluoropolymer for offshore applications. PRECISION POLYMER
ENGINEERING has
investigated the explosive decompression resistance of a low temperature
perfluoroelastomer including the effects of temperature and carbon
dioxide. The thermo-mechanical testing is often conducted separate to
environmental ageing and BAKER HUGHES has worked to combine the two to
simulate the in situ conditions for HPHT materials.
Steel pipes are coated
and lined to limit corrosion, insulate and ensure fluid flow. Robert
Walters has worked on the first subsea pipeline rehabilitation using a
composite-reinforced PVDF liner and SWAGELINING has used lining to prevent
internal corrosion in subsea pipelines and risers. For remediation,
ADVANCED COMPOSITE STRUCTURES AUSTRALIA and PETRONAS have cooperated in
developing a composite clamp system for the repair of high pressure
pipelines.
There is now long-term field experience of the
use of rubber hose/bonded flexible pipe: CONTITECH RUBBER INDUSTRIAL has
recovered and tested samples from several locations. Supercritical CO2 is
now commonly used for oil recovery and TECHNIP-FLEXIFRANCE has qualified
thermoplastic materials for use in flexible pipes transporting it.
PRYSMIAN SURFLEX UMBILICAIS E TUBOS FLEXÍVEIS DO BRASIL has evaluated the
thermal behaviour of high-strength tape reinforcement for flexible pipes.
There are high strength materials for ROV tether cables too, such as
DSM
DYNEEMA UHMWPE.
Element Oilfield Engineering with Polymers 2014
in London in October provides an international forum for advanced
technical discussions and offers unparalleled networking opportunities for
oilfield operators, contractors and their suppliers
Source: Dr Sally Humphreys, www.amiplastics.com
|
 Worldwide more than
90,000 paid subscriptions
Worldwide
more than 48,000 subscriptions - 100% one-year direct request
qualification
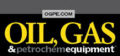
'What's New' in Upstream, Midstream and
Downstream Products & Services. Circulation 37,000
PennWell Petroleum Group:
Oil & Gas Journal
Oil & Gas Journal Russia
OGJ_eNewsletter OGJ-Website-Statistics
Oil, Gas & Petrochem Equipment
Offshore Magazine
Offshore
Russia
Offshore eNewsletter
Offshore
Website Statistics
Oil & Gas Financial Journal
+ + +
For more information, media
kits or
sample copies please contact
Andreas
Sicking +49 (0)2903-338570
wilhelms@pennwell.com
www.sicking.de
|