Siemens: Data-driven service enhances productivity, efficiency and quality
in the process industry
New service: Control Performance Analytics
Continuous analysis of process data for control loops Derivation of
recommendations for plant optimization Enhanced energy efficiency,
quality and productivity Fast setup according to the "plug & play"
principle
Oct. 07, 2014 + + + With Control Performance
Analytics, Siemens has presented a new data-driven service for the process
industry at the SPS IPC Drives show 2014. As part of this service, process
and status data from control loops are captured by the Simatic PCS 7
process control system. This data is analyzed by Siemens experts, who then
make recommendations for action. This gives companies transparency about
their control loops, enabling them to introduce targeted measures for
increasing efficiency, quality and throughput.
This service is particularly useful for
companies in the chemicals and pharmaceutical branches, food production,
as well as the oil and gas and glass and solar
industries.
Having optimal transparency with regard to control loops is a decisive
prerequisite for increasing the efficiency of plants in the process
industry. This is where Control Performance Analytics kicks in. Similar to
the "plug & play" principle, the new service can be quickly installed
during ongoing operation and the benefits reaped with a relatively small
financial investment. First of all a data collector, such as a nanobox, is
installed on site. This device captures process data from control loops
(for example process tags and alarms), previously defined by the user. It
then transmits the data to the Siemens Operation Center, adhering to
strict security standards all the time. The experts there then analyze the
data and make their evaluations available to the customer in the form of
reports via a web portal. These range from detailed analysis of individual
control loops, such as head temperatures of distillation columns and glass
trough temperatures, up to optimization recommendations for control loops
throughout the entire plant. This smart data analysis can be used to
identify increased energy consumption due to badly adjusted control loops,
for example. On the basis of evaluations, companies can introduce
selective measures to increase efficiency, quality and throughput. Exact
adjustment of the temperature of the glass trough can improve the quality
of the glass, for example, while simultaneously optimizing energy
consumption.
Thanks to its scalability and flexibility, this service is suitable for
companies of different sizes. The Basic Package offers continuous analysis
of control loops and their data defined together with the customer as well
as appropriate recommendations. If required, Siemens can support users
beyond this with the actual implementation of optimization measures.
Thanks to its Control Performance Analytics, Siemens has expanded its
range of Plant Data Services with its cloud-based acquisition and
evaluation of production data. Find more in
www.siemens.com/plant-data-services
Source: Dr. David Petry,
Siemens AG, Digital Factory Division
|
 Worldwide more than
90,000 paid subscriptions
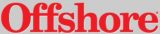 Worldwide
more than 48,000 subscriptions - 100% one-year direct request
qualification
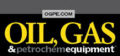
'What's New' in Upstream, Midstream and
Downstream Products & Services. Circulation 37,000
PennWell Petroleum Group:
Oil & Gas Journal
Oil & Gas Journal Russia
OGJ_eNewsletter OGJ-Website-Statistics
Oil, Gas & Petrochem Equipment
Offshore Magazine
Offshore
Russia
Offshore eNewsletter
Offshore
Website Statistics
Oil & Gas Financial Journal
+ + +
For more information, media
kits or
sample copies please contact
Andreas
Sicking +49 (0)2903-338570
wilhelms@pennwell.com
www.sicking.de
|