Trelleborg's new type of oil platform
Buoyed by success
Off the coast of Peru, the first of a new type of offshore platform for the offshore oil and gas industry has begun operation, and its setup may well revolutionize exploration and production around the world. Trelleborg’s role has been to make sure all the pieces fit together.
A new type of oil platform that is making its debut in the Pacific Ocean offshore Peru is expected to cut the cost and time involved in setting up new drilling operations across the industry. “The Buoyant Tower was designed to reduce the overall duration from offshore exploration to production by fabricating and installing a drilling and production platform in a short timeframe with reduced costs,” explains Bao Nguyen, Project Engineer at GMC Inc., one of the companies that developed the new design and managed the project. It could pave the way for a new generation of platforms that are simpler to make, easier and cheaper to install and that can be moved easily from location to location, anywhere in the world.
It took only 13 months to design, build and transport the BPZ Energy’s CX-15 production platform, the first platform using the Buoyant Tower concept, to the Peruvian Corvina field, where it is expected to produce 12,200 barrels of oil and 12.8 million standard cubic feet of gas per day. The concept was developed by HortonGMC, a joint venture between Horton Wison Deepwater and GMC Inc.
The Buoyant Tower hull consists of four cylindrical tubes with one central suction pile. Each cell measures 26 feet (8.4 meters) in diameter and 197 feet (60 meters) in length. The central suction pile, integral to the hull structure, attaches the structure to the seabed. On top of the 2,500-ton Buoyant Tower hull sits a 1,500-ton platform where the production drilling is carried out.
A critical operation is the float-over, which involves placing the production platform over the tower and then connecting the two together. Trelleborg supplied the leg mating units (LMU) and deck support units (DSU) for the project. An important aspect of Trelleborg’s design was to help dampen the loads while performing the float-over. “The company’s customer service and track record were key contributors to being selected,” Nguyen says.
JP Chia, Engineering Manager at Trelleborg Offshore & Construction in Singapore, explains: “The design turnaround time was critical in order to meet the installation schedule. Installation took place in the open sea where there are rough sea conditions and high swell, and the float-over window period was very limited. With such critical factors, the LMU and DSU designs was modeled accurately with our in-house finite element analysis.”
“Trelleborg was able to fulfill the design and delivery process within four months – a record,” adds Vincent Tan, Sales and Marketing Manager within Trelleborg Offshore & Construction.
Nguyen explains that a major benefit and cost saving for the Buoyant Tower design was that only one major construction vessel was needed for the installation procedure. “One vessel acts as both the heavy transportation vessel and the main construction vessel,” he says. “Traditionally fixed structures need a transportation vessel and an expensive derrick barge to perform heavy lifts for installation. This project was the first cantilevered float-over operation from a heavy transportation vessel. The motions of the transportation vessel and the design of the cantilever structure had to be thoroughly evaluated.
“The structure is suited for water depths between 50 and 280 meters [165 to 920 feet] in any type of field with any type of reservoir characteristics – gas, oil or a combination,” he says. “The drilling and/or production equipment can be modularized to adapt to the needs of the operation. The Buoyant Tower is well suited for regions of seismic activity, and in this case the compliant behavior of the tower can resist seismic loads better than a traditional fixed platform. Plus, the Buoyant Tower can be relocated to new fields, requiring less overall capital expenditure to bring a field online.”
The design of the tower is based on existing cell spar technology that has been proven in offshore productions worldwide. The simple structure translates into easier fabrication assembly. Following the success of the Peruvian project, the design is being evaluated for use in all major regions of the world.
For more information
news@trelleborg.com | www.trelleborg.com
Posted: Sept. 04, 2013
|
.
Worldwide more than 100,000 paid subscriptions
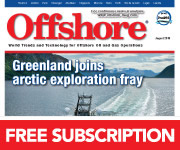 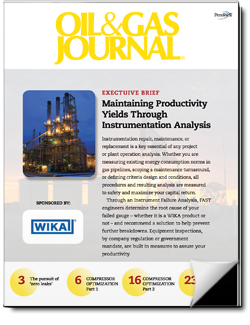 Technical
Briefs from the editors of Oil & Gas Journal and Offshore Magazine: Click
here ... and see what we have designed, produced, published and promoted for WIKA
and FMC Technologies ... and what we would like to do for you.
.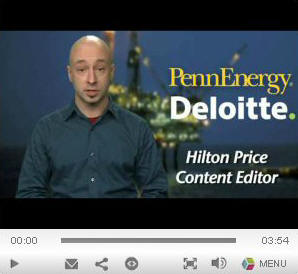 PennEnergy
Weekly Video News
.PennWell Petroleum Group:
OGJ - Oil & Gas Journal
OGJ_eNewsletter
Offshore Magazine
Offshore eNewsletter
Oil & Gas Financial Journal
Oil, Gas & Petrochem
OGJ Russia
OGJ LatinoAmericana
PennEnergy PennEnergy-eNewsletter
+ + +
For more information, media
kits or
sample copies please contact
wilhelms@pennwell.com
www.sicking.de
|